Our R&D team in Marysville, Ohio, knows all too well the mantra of ScottsMiracle-Gro co-founder Horace Hagedorn: “Find a need and fill it.” Typically their work along these lines takes the form of developing innovative lawn and garden products and solutions for consumers.
But when the COVID-19 pandemic hit, they put their skills to another test, all in an effort to help their fellow associates working on the front lines stay safe.
“We literally took our R&D Formulation Barn and turned it into a manufacturing operation for hand sanitizer,” said Paula Powell, Director, Hydroponic Nutrition & Controls R&D for ScottsMiracle-Gro.
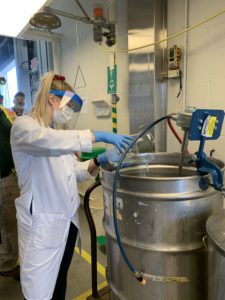
The Marysville Formulation Barn houses laboratories where R&D chemists and engineers develop and test lawn and garden products. They were in the midst of conducting trials for new products slated to launch later this year when they were approached about a problem facing their colleagues in supply chain and sales.
These teams were having trouble finding enough hand sanitizer to stay safe, and the question was raised as to whether or not our own R&D team could produce it.
“We pretty quickly dove into figuring out how to make it happen,” said Janelle Restum, VP, Global Regulatory Affairs. “It’s been impressive to see people come together, figure out how to do this and get down to solving the problem.”
Within a week and a half, the team went from receiving the request to shipping bottles out the door. One of the first steps was developing the right formulation, which they were able to adapt from a World Health Organization recipe. To be effective, hand sanitizer must contain at least 75 percent isopropyl alcohol. Our hand sanitizer is a blend of isopropyl alcohol, hydrogen peroxide, glycerin and water.
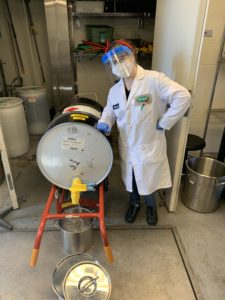
Then, they had to source the raw materials and bottles at a time when many of these things were sold out. Through a lot of hard work and investigation, members of our supply chain and procurement teams were able to secure all of the materials, including the 32-ounce bottles, from facilities within our own organization. The materials were diverted from their original uses to be used for the hand sanitizer project.
Next came the manufacturing and bottling process, which was a manual undertaking completed by a small group of our R&D associates. To make hand sanitizer, they had to follow stringent safety and environmental procedures and monitoring. They used social distancing and wore personal protection equipment, including face shields. Air quality was monitored to ensure there were no excessive vapors. Fans were run to enhance ventilation.
Once the R&D team had liquid sanitizer, they spent hours each day filling and labeling bottles. They then packed them for shipment to their fellow associates. Approximately 1,150 bottles were shipped for use by associates in our manufacturing plants and field sales team.
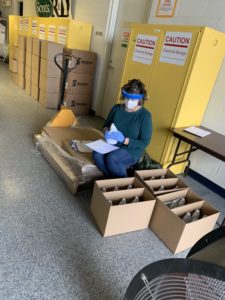
“This delivery was really appreciated,” said John Hooper, Plant Manager in Harrisonville, Missouri. “We, as everyone else, had been unsuccessful searching online and at local stores for available inventory. Plus, we really didn’t want to be out there shopping in all those stores. The hand sanitizer came in the nick of time. A heartfelt thanks from the team in Harrisonville.”
In times like these, we’re proud of our associates who came together through innovation, creativity and the desire to help out their fellow colleagues. Thanks to all of our associates in R&D and Environmental, Health & Safety who played a role in making this happen.