Operating sustainably
We operate by our values. This means incorporating sustainability into all aspects of our supply chain.
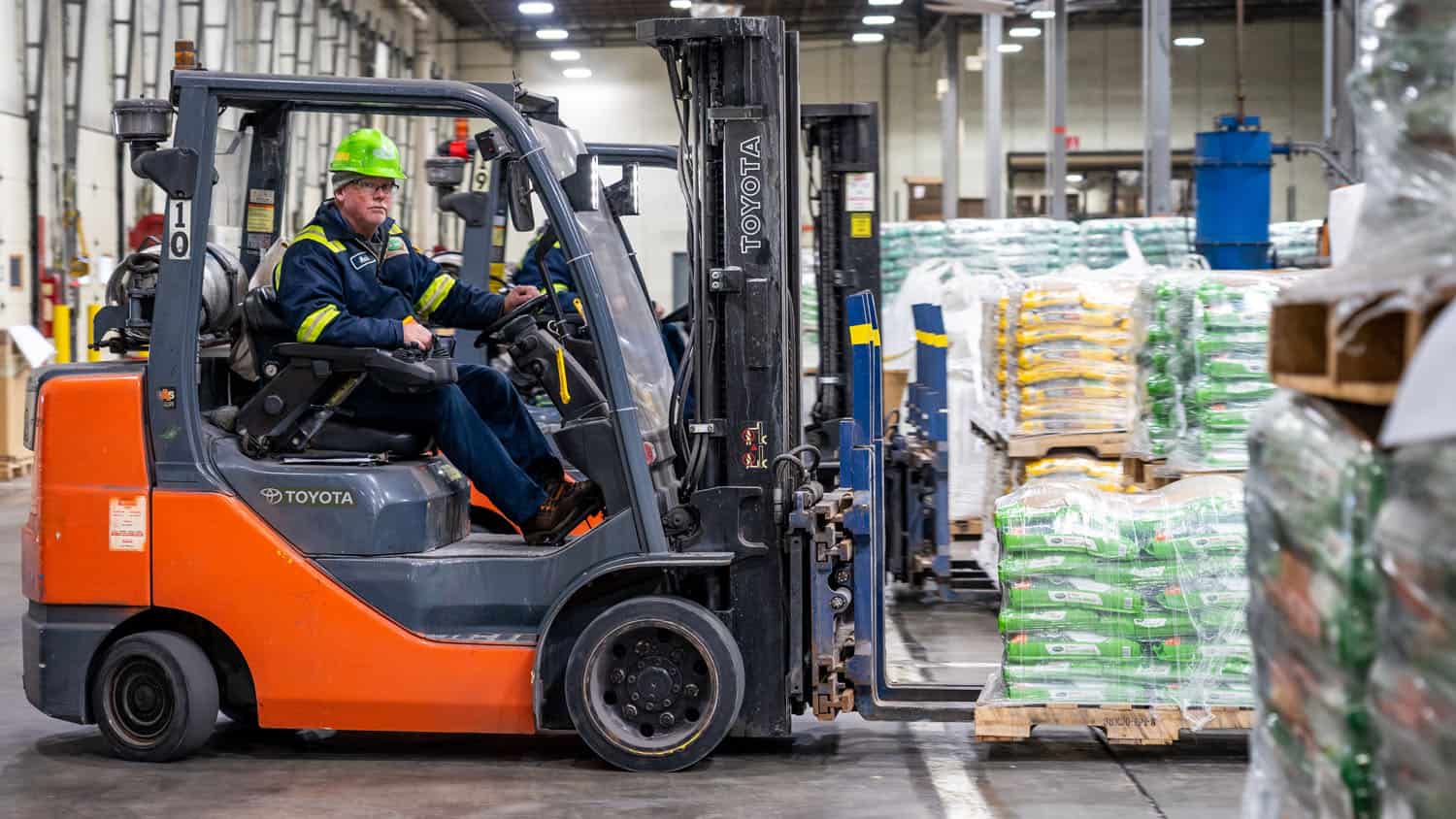
Health and safety
The safety of our associates is our top priority. We implement rigorous health and safety procedures customized to each workplace.
Green waste recycling
As a leading user of compost in North America, we embrace our unique ability to drive circularity. We recycled roughly 5.5 billion pounds of green waste locally in 2023.
Water
To be responsible water stewards, we explore ways to reduce the amount of water we use in our manufacturing and reduce our water-related impacts on local communities.
Energy and emissions
We aim to reduce negative impacts to the environment stemming from our energy usage and emissions generation.